THERMAL SAND RECLAMATION PLANT

Thermal sand reclamation plant
The entire plant is composed by a vibrating crusher FSV type for the reduction in size and the screening of sands, a pneumatic conveying system, which transport the material to the storage silos and, between them, a deferrization system for the material.
From the storage silos, the material is conveyed, through a pneumatic conveying system, to the process furnace called FEUER, thermally treated and equipped with volumetric feeding.
Then the system includes a fluid bed cooler, with diathermic oil cooling circuit, and a consequent transport of the material to the storage silos.
A pneumatic and electrical panel with touch-screen operator interface controls the entire system.
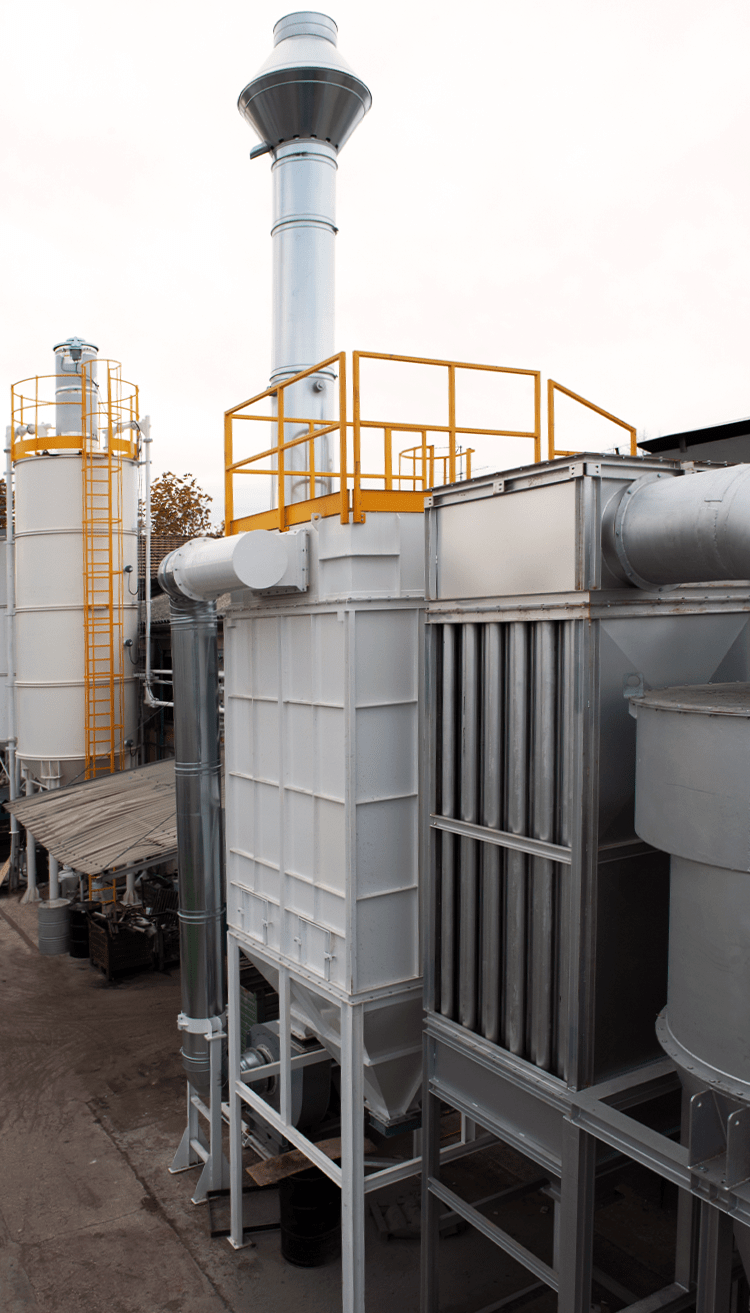
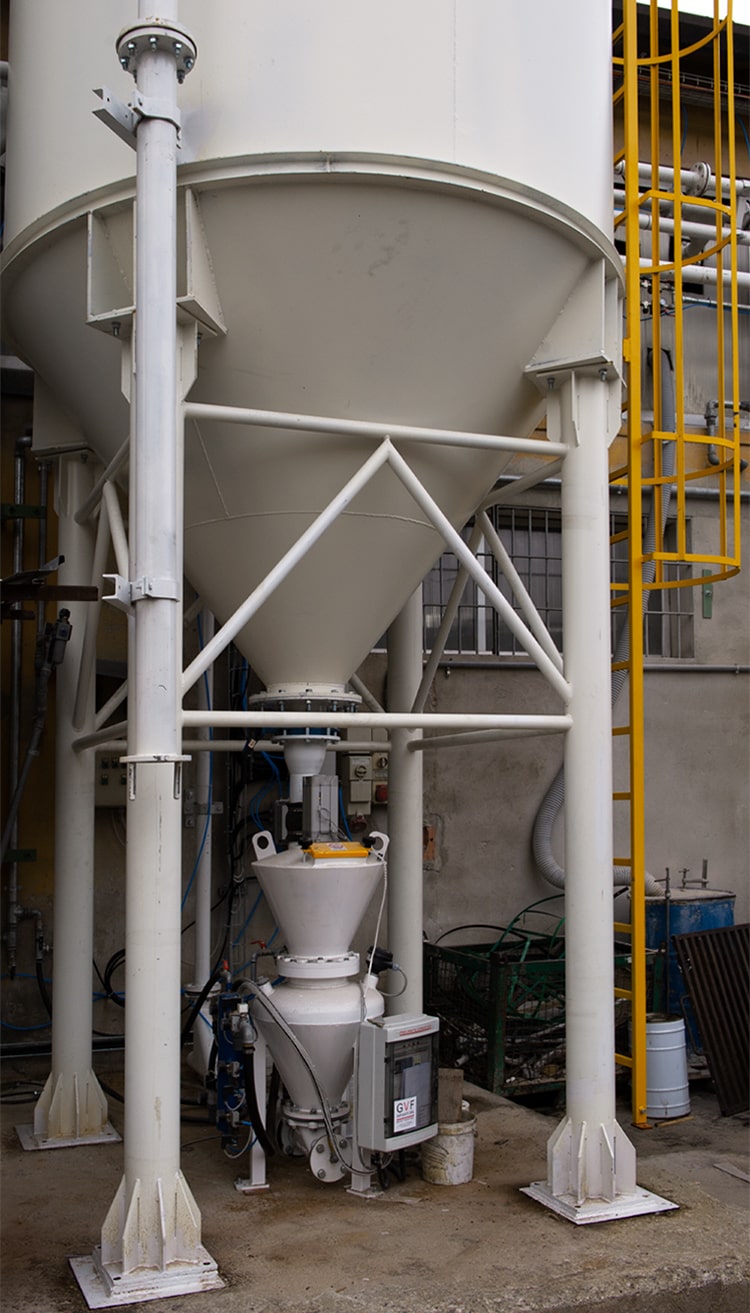
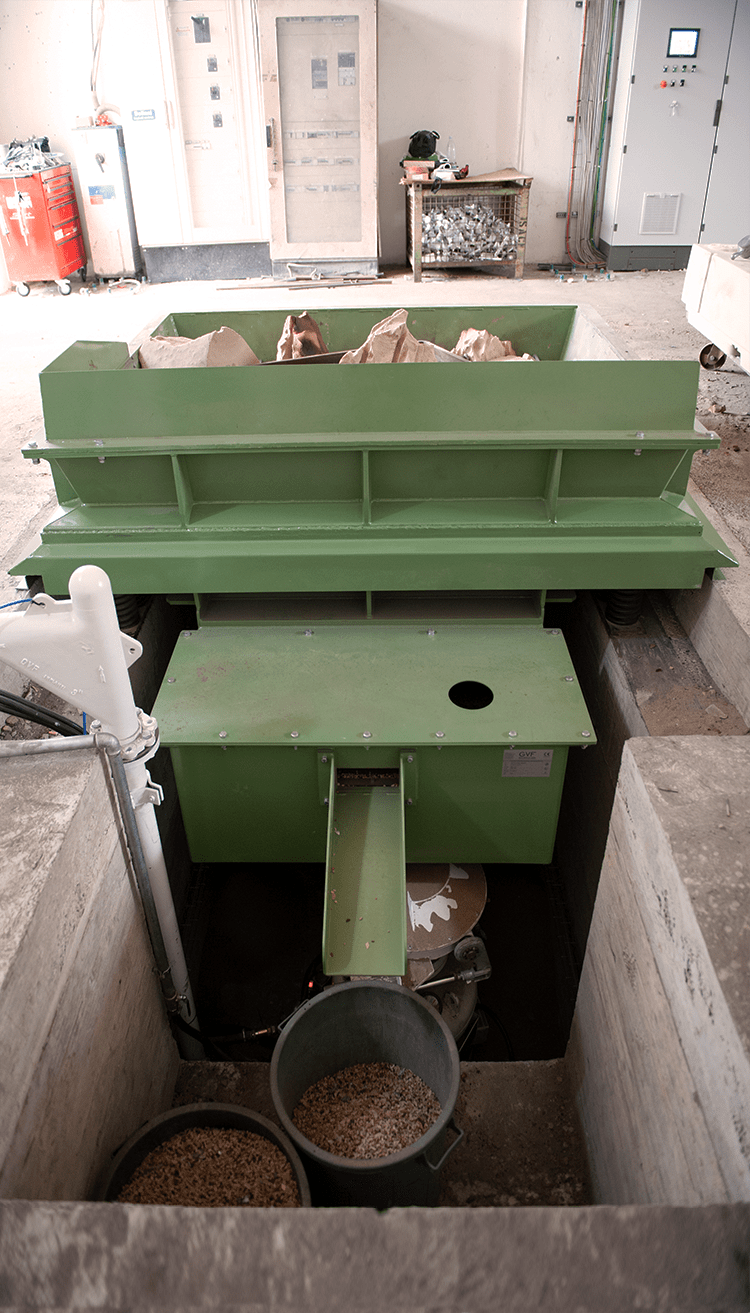
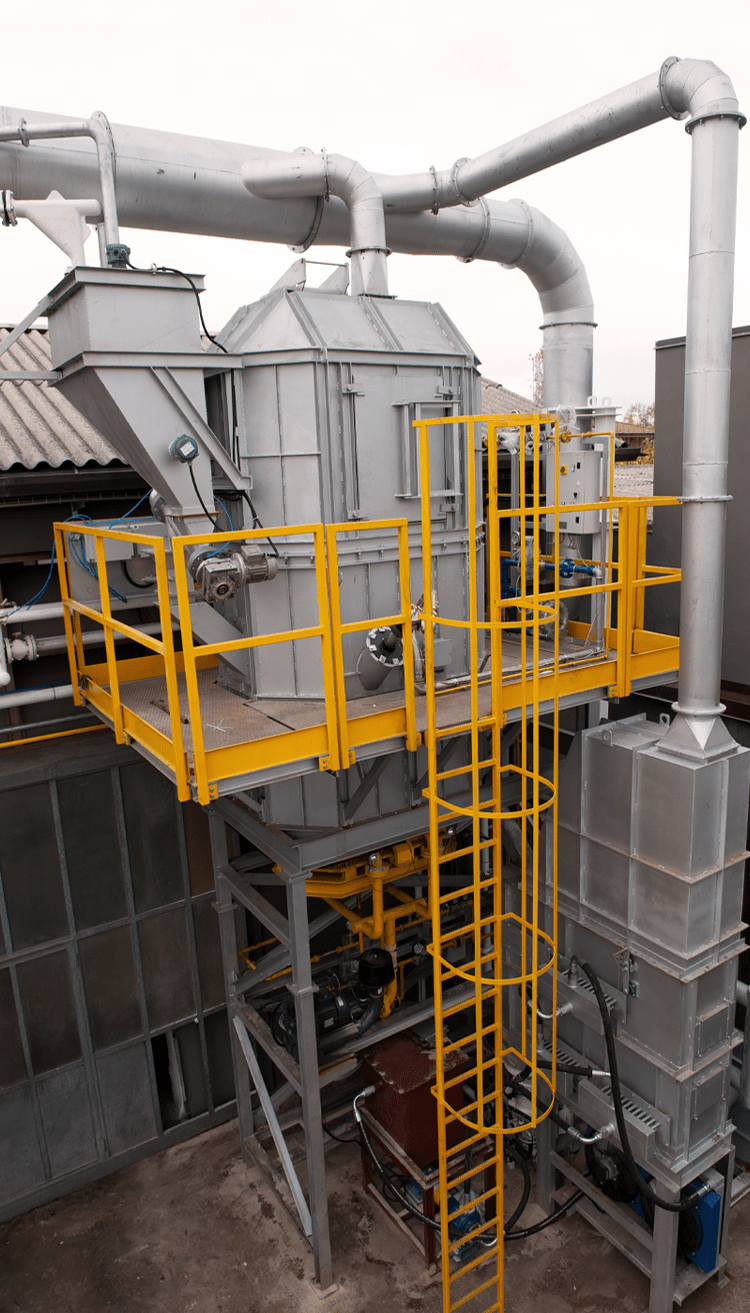

Sand Treatment
TECHNICAL DATA
GVF Impianti’s thermal sand reclamation plants are turn-key supplied and they include all the machines from the sand crushing to the sand reclamation up to the effluents treatment.
FEUER THERMAL SAND RECLAMATION

The fluid bed is created at a precise height from the bottom and at a right distance from the containment tank, in order to guarantee a heat protection to the whole structure.
The product is then divided through an especially shaped wall, so to resist to thermal expansion, made in stainless steel for high temperature.
This allows the protection of the inner covering, which is made by mats made in eco-friendly material, following the current regulation, that are not worne out by the sand friction.
The fluid bed is divided into more than one section, in order to adjust the temperatures in a differentiated way, improving the efficiency of the machine and giving a notable saving in energy.
The entire working cycle is controlled by two series of temperature probes, which guarantee the perfect functioning and the continuous control of the temperatures, in order to prevent plastic effects of the material.
Each air injection is controlled by a digital differential manostat, which supervise the correct functioning of the machine, pointing out also possible functioning anomaly. The big gas expansion chamber, allows the complete combustion, respecting the current regulation if the conduction stays within the minimum designed temperature limits of the fluid bed.
A post-combustor is installed on request, and it is supplied complete with output temperature control and with a continuous oxygen detection system.
The machine is totally automatic and easy to manage; the touch screen operator interface allows to have the complete control of the system in few steps.
Particularly inexpensive for what concerns its management and maintenance, it is a necessary choice for the foundry’s sand management systems.
This machine is the heart of the treatment plant, and it has a combustion system which allows to remove the resins from the treated material, guaranteeing a sand’s high quality. The project developed by the GVF Impianti Srl technicians, is backed by 50 years of experience in sand reclamation furnace engineering.
The new fluid bed lowers considerably the management costs of the plant thanks to a mix injection nozzles’ special design and to their widespread distribution over the fluid bed.
The two plenums, air and gas, are divided so that mix sacks are avoided and the gas’ plenum is isolated from the machine. The Gas-Air mix is created inside the nozzle just before it is injected into the fluid bed and this process is performed with a high speed, so that a perfect combustion of the gas and the maximum output of the whole system are guaranteed.

LOW CONSUMPTION
NEW ARIA-GAS NOZZLES
WEAR-RESISTANT CONSTRUCTION
INNOVATIVE BURNING SYSTEM
DIFFERENTIATED TEMPERATURE SETTING
Fluid Bed Cooler
Air - Oil cooling circuit
The study of these problems has led to the deveolpment of a range of machines from 0,5 to 30 T/h, composed by three or more fluid beds, crossed in counter-current by air and refrigerated by a diathermic oil circuit, filled by a pump and by a forced refrigerating unit.
This design allows to obtain a high efficiency of the system, the lack of blockages due to the limestone and the lack of liquid spillages, thanks to the fact that the cycle is totally closed.


On request the oil circuit can be completed with a forced refrigerating system through a chiller, which in turns allows decreasing significantly the outlet sand’s temperature.
The upper part of the machine forms a big suction hood at low speed, in order to reduce to a minimum the forced extraction of sand. Into this hood are directed all the reliefs of each level through specific ducts.
Maintenance free, high efficiency and modular management make this machine the best cooling response of foundry sands.
CLOSED COOLING CIRCUIT
NO WATER OR LIMESTONE
CROSSED FLOWS COOLING SYSTEM
HIGH EFFICINECY
HIGH LEVEL OF DUST REMOVAL
POSSIBLE CHILLER ADDITION
result of the regeneration process
IMPROVEMENT IN THE SAND’S GEOMETRIC SHAPE
BINDER CONSUMPTION OPTIMIZATION
CAST QUALITY IMPROVEMENT
LOW ACID DEMAND VALUE
PERMEABILITY IMPROVEMENT
NO THERMAL EXPANSION
ALMOST NO LOSS ON IGNITION
REDUCE COSTS AND ENVIRONMENTAL IMPACT BY IMPROVING THE QUALITY OF SAND.
FINE PARTICLES REMOVAL
The fine particles generated during the foundry sand processing cycle are removed thanks to the “tailor-made” sand reclamation process.
THERMAL EXPANSION
No grain’s thermal expansion.
LACK OF IMPURITY
Through the reclamation process, the impurities inside the used sand are removed.
GRAIN ROUNDNESS
The grains’ surface becomes more rounded, requiring a lower quantity of binders.
ACID DEMAND VALUE
Low Acid Demand Values.
LOW LOSS ON IGNITION
Practically no loss on ignition.

used sand

reclaimed sand
best practices in sand treatment

FSV VIBRATING CRUSHER
The high performance vibrating crusher works with the sand over sand theory, and crushes the agglomerated sand until it has reduced the sand to the needed sizes for the thermal reclamation. Capacity from 0,5 to 3 Ton/h.
The machine is composed by a wide crushing hopper, which has replaceable wear-resistant armored sides and a grill with particular crossed shapes for the primary selection of the sand.
The material crushed in this way, moves to a secondary crushing chamber, which has a selection stainless steel grill, and in which all the metal small impurities are stopped and wasted.
The machine is equipped with inspection and rear unloading door, fast-lock system of the selection grills and lateral outlet door for the waste.
EXTRA-DENSE PHASE PNEUMATIC CONVEYORS
GVF Impianti Srl produces dense phase pneumatic conveying systems since more than 55 years with different sizes and volumetric capacities from 24 to 4.000 lt. The experience gained in several years of works and in a lot of applications with different materials has led to the development of a wide range of conveyors’ models. In foundry sands transport the GC model with a wear-resistant cone loading valve is normally used. The two-ways or multi-ways diverting systems (up to 12 ways), the wear-resistant bends, the wear-resistant terminal boxes and the silos’ top diverting systems complete the production range. All the machines are supplied complete with their electro-pneumatical control panel.
EXTRA-DENSE PHASE PNEUMATIC CONVEYORS
GVF Impianti Srl produces dense phase pneumatic conveying systems since more than 55 years with different sizes and volumetric capacities from 24 to 4.000 lt. The experience gained in several years of works and in a lot of applications with different materials has led to the development of a wide range of conveyors’ models. In foundry sands transport the GC model with a wear-resistant cone loading valve is normally used. The two-ways or multi-ways diverting systems (up to 12 ways), the wear-resistant bends, the wear-resistant terminal boxes and the silos’ top diverting systems complete the production range. All the machines are supplied complete with their electro-pneumatical control panel.

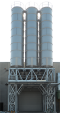
SILOS AND STORAGE SYSTEMS
We produce and supply material storage systems complete with filling and extraction systems. From the supply of a single silo up to the supply of storage silos’ sets, complete with accessories such as level probes, relief valves, silo’s top filters, loading systems from truck, silos’ weighing systems and silos’ weight in loss discharging systems. These are only some of the possible configurations supplied. Inside the silos’ discharging systems range, GVF Impianti produces silos’ cone fluidizing systems through vibrating fluidizing nozzles or through pulse-jet fluidizing systems and vibrating cones. The installations are equipped with discharging butterfly valves or with discharging double chamber valves depending on the applications’ type and they can be supplied with truck loading bellows.
Phone

